Advanced Multi-Sample Bead Fusion System for Precise XRF Analysis with Integrated LOI/LOF Measurement
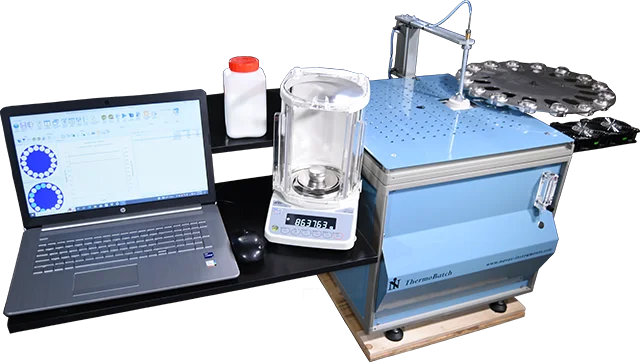
Introducing Navas Instruments FTA-2000 (Fusion Thermogravimetric Analyzer)
Our patented bead fusion machines integrate state-of-the-art features to revolutionize XRF sample preparation. Designed for precision and simplicity, the system is built on the foundation of a multi-sample thermogravimetric analyzer and incorporates advanced automation and weighing capabilities for unmatched accuracy and efficiency.
Our bead fusion machines may appear complex at first glance, but they are designed for effortless operation. The instrument autonomously handles all procedures, ensuring a seamless user experience.
Our bead fusion systems are compact and designed to fit comfortably on a tabletop.
Our instruments are designed for performance. Their appearance reflects robust construction, mechanical precision, and long-term durability—essential qualities for reliable operation in demanding cement and mining environments.
Operational Overview of Bead Fusion in Our Instrument
The system uses two high-precision digital balances, both with a sensitivity of 0.1 mg. Both balances are directly connected to the PC, allowing weights to be automatically recorded and managed by the software, ensuring seamless and accurate data capture throughout the process.
Operational Overview of Bead Fusion in Our Instrument
The system uses two high-precision digital balances, both with a sensitivity of 0.1 mg. Both balances are directly connected to the PC, allowing weights to be automatically recorded and managed by the software, ensuring seamless and accurate data capture throughout the process.
Internal balance
Located beneath the furnace, this balance measures crucible weights at high temperatures (Typically 1050°C) during the fusion process. The balance pedestal passes through a small orifice in the bottom of the furnace to ensure precise weight measurements in real time.
Internal balance
Located beneath the furnace, this balance measures crucible weights at high temperatures (Typically 1050°C) during the fusion process. The balance pedestal passes through a small orifice in the bottom of the furnace to ensure precise weight measurements in real time.
External balance
Used by operators for initial weighing of crucibles, samples, and flux. Crucibles can also be pre-weighed for convenience.
External balance
Used by operators for initial weighing of crucibles, samples, and flux. Crucibles can also be pre-weighed for convenience.
An internal and an external balance for precise sample weighing
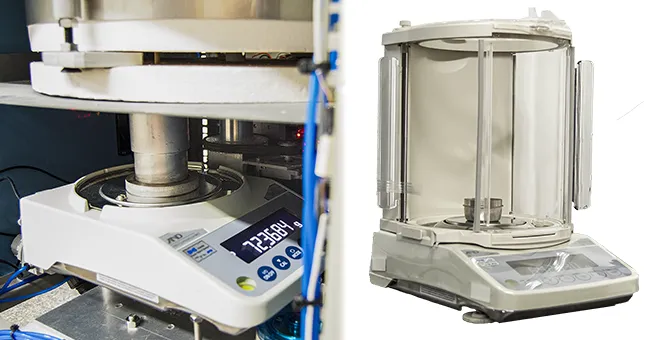
Furnace Carousel with Enhanced Precision and Mixing Capabilities
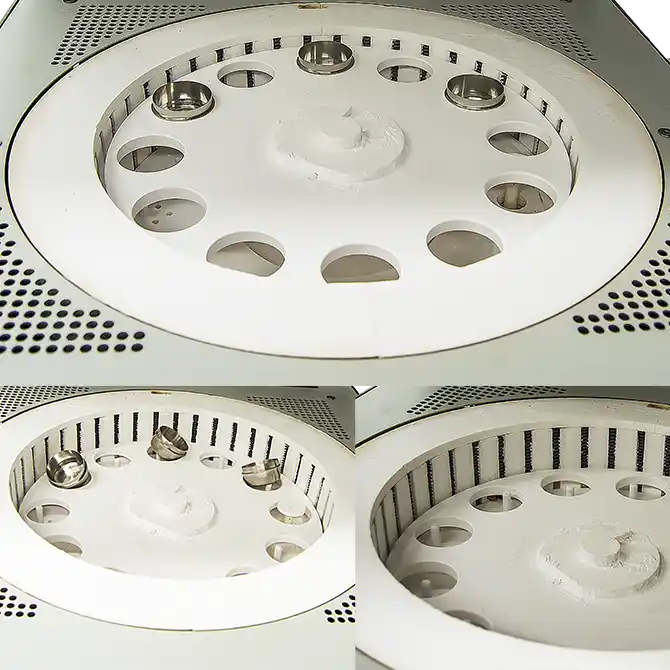
Furnace Carousel with Enhanced Precision and Mixing Capabilities
The furnace features a carousel with a capacity ranging from 4 to 16 crucibles, providing exceptional precision and versatility
The carousel raises, rotates, and lowers to accurately position crucibles over the internal balance for precise weight measurements during fusion.
It also tilts and agitates crucibles to mix samples and flux thoroughly. A ring with pins at the bottom of the furnace facilitates this mixing.
Furnace Carousel with Enhanced Precision and Mixing Capabilities
The furnace features a carousel with a capacity ranging from 4 to 16 crucibles, providing exceptional precision and versatility
The carousel raises, rotates, and lowers to accurately position crucibles over the internal balance for precise weight measurements during fusion.
It also tilts and agitates crucibles to mix samples and flux thoroughly. A ring with pins at the bottom of the furnace facilitates this mixing.
Fully Automated Sample Handling and LOI Calibration for Enhanced Efficiency
An auto-loader or sample handler equipped with a 12- or 16-crucible capacity, designed for seamless loading and unloading.
Software allows calibration of the LOI of the flux by fusing a bead made solely of flux, without sample, to determine its LOI. Optionally, the user can include an additional crucible containing only flux in each batch to calculate and correct the LOI of the flux for that specific batch, ensuring consistent accuracy across all samples.
Fully automated operation requires minimal operator involvement, ensuring efficiency and ease of use. The initial weights are automatically recorded by the computer from the external balance. The operator simply places the crucible on the balance and presses the Enter key to record its weight. Next, the sample is added to the crucible, and its weight is recorded in the same way, followed by the addition of flux, whose weight is similarly recorded.
For added convenience, crucibles can be pre-weighed, eliminating the need for weighing them during the process. Optionally all data, including weights, sample identification codes, and other relevant information, can be seamlessly imported from text or CSV files, further streamlining the workflow. Once the initial data is recorded, the process is entirely automated, making the system exceptionally user-friendly and efficient.
Configurable automatic bead cooling, activated after all beads are transferred to the auto-loader.
Fully Automated Sample Handling and LOI Calibration for Enhanced Efficiency
An auto-loader or sample handler equipped with a 12- or 16-crucible capacity, designed for seamless loading and unloading.
Software allows calibration of the LOI of the flux by fusing a bead made solely of flux, without sample, to determine its LOI. Optionally, the user can include an additional crucible containing only flux in each batch to calculate and correct the LOI of the flux for that specific batch, ensuring consistent accuracy across all samples.
Fully automated operation requires minimal operator involvement, ensuring efficiency and ease of use. The initial weights are automatically recorded by the computer from the external balance. The operator simply places the crucible on the balance and presses the Enter key to record its weight. Next, the sample is added to the crucible, and its weight is recorded in the same way, followed by the addition of flux, whose weight is similarly recorded.
For added convenience, crucibles can be pre-weighed, eliminating the need for weighing them during the process. Optionally all data, including weights, sample identification codes, and other relevant information, can be seamlessly imported from text or CSV files, further streamlining the workflow. Once the initial data is recorded, the process is entirely automated, making the system exceptionally user-friendly and efficient.
Configurable automatic bead cooling, activated after all beads are transferred to the auto-loader.
Fully Automated Sample Handling and LOI Calibration for Enhanced Efficiency
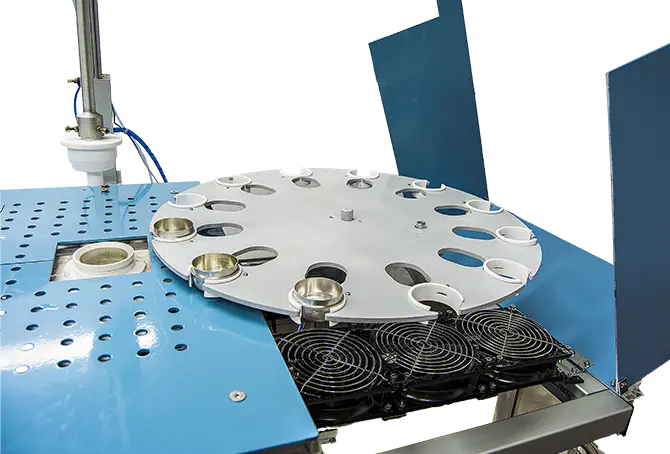
Key Features and Benefits
Eliminating Fusion Variability with Innovative Design
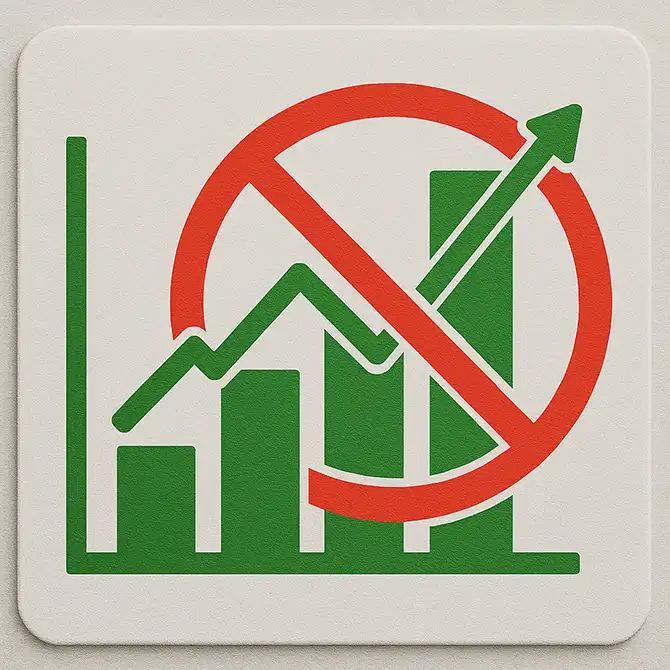
Eliminating Fusion Variability with Innovative Design
Traditional fusion machines rely on flux containing a high quantity of non-wetting agents (e.g., lithium bromide).
During fusion, these agents evaporate unpredictably depending on time and temperature, leading to variability in fusion weights.
Such systems require complex calculations and predictions to estimate the evaporation, making the process uncertain and potentially affecting XRF analysis results.
Our solution: By using a peristaltic pump to automatically add a small, controlled amount of non-wetting agent diluted in water after the final bead weight of each sample is measured, our system ensures consistent fusion weights without the need for additional calculations, guaranteeing accurate results every time.
Eliminating Fusion Variability with Innovative Design
Traditional fusion machines rely on flux containing a high quantity of non-wetting agents (e.g., lithium bromide).
During fusion, these agents evaporate unpredictably depending on time and temperature, leading to variability in fusion weights.
Such systems require complex calculations and predictions to estimate the evaporation, making the process uncertain and potentially affecting XRF analysis results.
Our solution: By using a peristaltic pump to automatically add a small, controlled amount of non-wetting agent diluted in water after the final bead weight of each sample is measured, our system ensures consistent fusion weights without the need for additional calculations, guaranteeing accurate results every time.
High-Precision Weighing Made Effortless for Operators
Competitor systems function as simple furnaces and do not incorporate any weight measurement capabilities.
In competitors' systems, the evaporation of flux LOI and the mass loss of non-wetting agent during fusion are unpredictable, depending on time and temperature. This requires calculations or predictions to adjust for weight changes, further increasing complexity and the chance for error.
Our solution: Both the internal and external balances in our system provide high-precision weight measurements. Unlike competitors' instruments, which require operators to weigh samples and flux with a strict tolerance of ±0.3 mg, our system allows a much broader tolerance of ±30 mg by eliminating the variables that impact accuracy and automatically determining flux LOI. This innovation eliminates the tedious and time-consuming weighing process, significantly reducing operator effort while maintaining exceptional accuracy.
Both balances—internal (beneath the furnace) and external (used for initial weights)—are directly connected to the computer, ensuring precise and reliable weight measurements throughout the entire process.
High-Precision Weighing Made Effortless for Operators
Competitor systems function as simple furnaces and do not incorporate any weight measurement capabilities.
In competitors' systems, the evaporation of flux LOI and the mass loss of non-wetting agent during fusion are unpredictable, depending on time and temperature. This requires calculations or predictions to adjust for weight changes, further increasing complexity and the chance for error.
Our solution: Both the internal and external balances in our system provide high-precision weight measurements. Unlike competitors' instruments, which require operators to weigh samples and flux with a strict tolerance of ±0.3 mg, our system allows a much broader tolerance of ±30 mg by eliminating the variables that impact accuracy and automatically determining flux LOI. This innovation eliminates the tedious and time-consuming weighing process, significantly reducing operator effort while maintaining exceptional accuracy.
Both balances—internal (beneath the furnace) and external (used for initial weights)—are directly connected to the computer, ensuring precise and reliable weight measurements throughout the entire process.
Enhanced Productivity and Accuracy
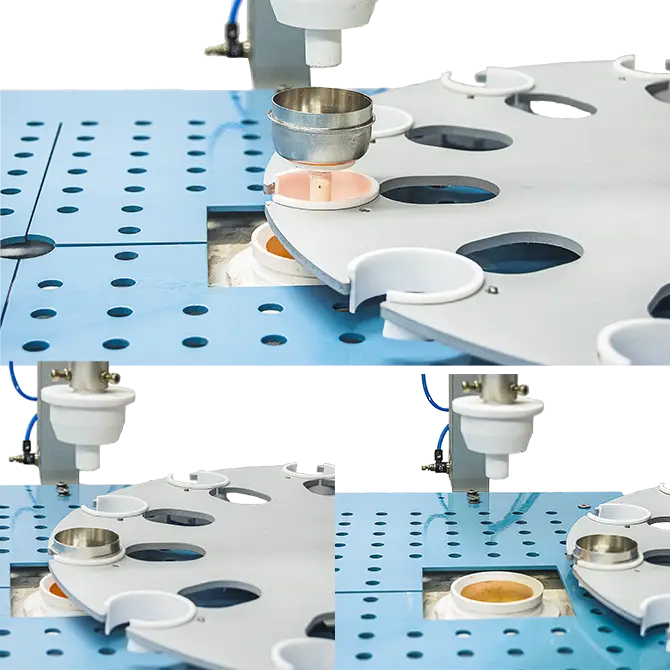
Enhanced Productivity and Accuracy
Electric furnace fuses from 4 up to 16 beads in just 20–25 minutes, significantly increasing throughput.
Simultaneous production of fused beads and LOI/LOF measurements minimizes bias, as the same sample is used for both processes.
Detailed sample weights and real-time charts are provided for each bead, enabling the operator to monitor weight stability and determine precisely when the sample fusion is complete. This ensures no unnecessary fusion time is added, allowing for shorter fusion cycles and increased laboratory productivity.
Enhanced Productivity and Accuracy
Electric furnace fuses from 4 up to 16 beads in just 20–25 minutes, significantly increasing throughput.
Simultaneous production of fused beads and LOI/LOF measurements minimizes bias, as the same sample is used for both processes.
Detailed sample weights and real-time charts are provided for each bead, enabling the operator to monitor weight stability and determine precisely when the sample fusion is complete. This ensures no unnecessary fusion time is added, allowing for shorter fusion cycles and increased laboratory productivity.
Cost Efficiency and Space Savings
One instrument performs both bead fusion and LOI/LOF analysis, reducing equipment needs and freeing up laboratory space.
No additional thermogravimetric analyzer (TGA) is required, unlike competitors' systems, which typically involve significant costs and analysis times exceeding two hours for LOI determination. This also reduces the laboratory space needed, optimizing operational efficiency.
No glass bead pouring is required, minimizing platinum-ware use and reducing costs.
No crucible cleaning is required after each batch, as the system eliminates the need for pouring molten material, preventing residue buildup and cross-contamination. This significantly reduces operator time and effort.
Cost Efficiency and Space Savings
One instrument performs both bead fusion and LOI/LOF analysis, reducing equipment needs and freeing up laboratory space.
No additional thermogravimetric analyzer (TGA) is required, unlike competitors' systems, which typically involve significant costs and analysis times exceeding two hours for LOI determination. This also reduces the laboratory space needed, optimizing operational efficiency.
No glass bead pouring is required, minimizing platinum-ware use and reducing costs.
No crucible cleaning is required after each batch, as the system eliminates the need for pouring molten material, preventing residue buildup and cross-contamination. This significantly reduces operator time and effort.
Cost Efficiency and Space Savings
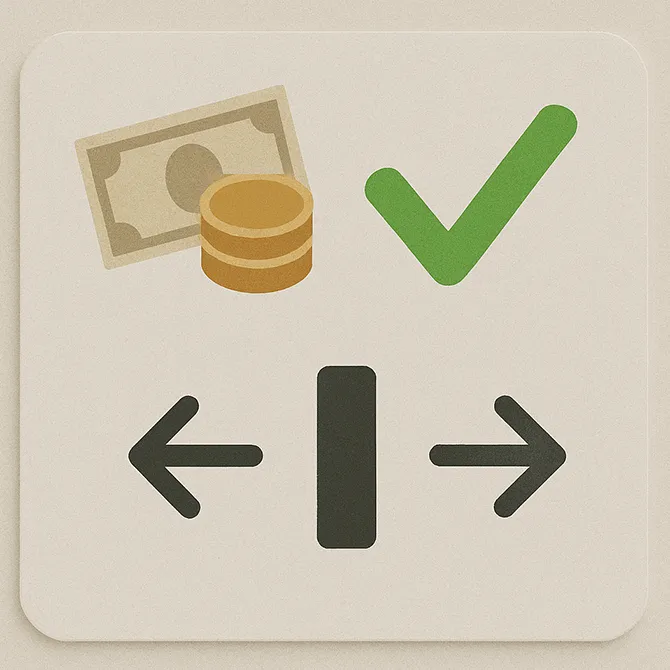
Operator and Environmental Safety
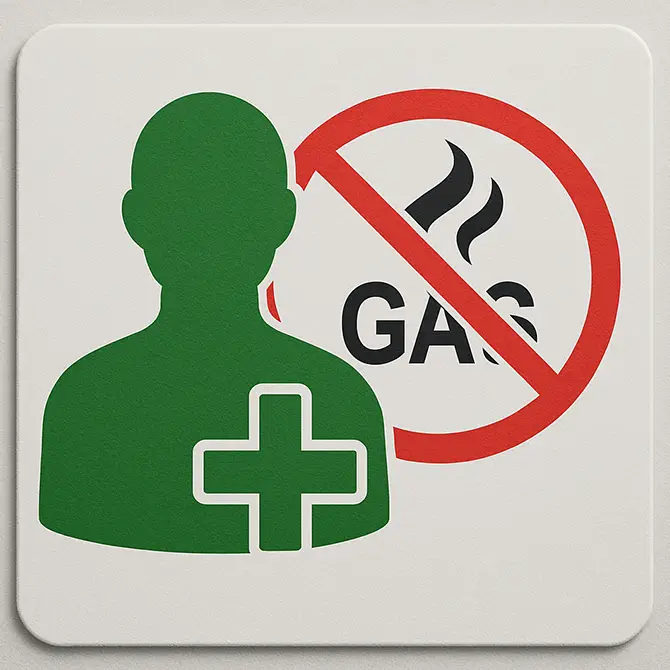
Operator and Environmental Safety
Minimal toxic gas emissions are achieved through the use of a peristaltic pump, which automatically adds a small, controlled amount of non-wetting agent diluted in water at the end of the fusion process, after the final bead weight of each sample is measured. This approach eliminates the need for flux containing large amounts of non-wetting agent, significantly reducing exposure to harmful vapors during fusion.
Reduced health exposure and minimal gas emissions align with sustainable lab practices.
Operator and Environmental Safety
Minimal toxic gas emissions are achieved through the use of a peristaltic pump, which automatically adds a small, controlled amount of non-wetting agent diluted in water at the end of the fusion process, after the final bead weight of each sample is measured. This approach eliminates the need for flux containing large amounts of non-wetting agent, significantly reducing exposure to harmful vapors during fusion.
Reduced health exposure and minimal gas emissions align with sustainable lab practices.
Automation and Usability
The fully automated system enables overnight, unattended operation, significantly increasing productivity and efficiency. When integrated with the optional collaborative robotic arm, the process is entirely hands-free. The system includes a conveyor with trays holding glass vials that contain pre-weighed samples and flux. The robot pours the contents of each vial into crucibles positioned on the auto-loader. Once filled, the crucibles are automatically transferred into the furnace, where the samples are fused.
After fusion, the crucibles are automatically returned to the auto-loader, and the robot automatically transfers the resulting beads into the XRF spectrometer for analysis. The spectrometer is triggered automatically to perform the analysis. Once completed, the robot retrieves the analyzed beads from the XRF spectrometer and discards them into a bin. This seamless automation streamlines the entire process, enabling consistent, high-throughput operation with minimal operator intervention.
Automation and Usability
The fully automated system enables overnight, unattended operation, significantly increasing productivity and efficiency. When integrated with the optional collaborative robotic arm, the process is entirely hands-free. The system includes a conveyor with trays holding glass vials that contain pre-weighed samples and flux. The robot pours the contents of each vial into crucibles positioned on the auto-loader. Once filled, the crucibles are automatically transferred into the furnace, where the samples are fused.
After fusion, the crucibles are automatically returned to the auto-loader, and the robot automatically transfers the resulting beads into the XRF spectrometer for analysis. The spectrometer is triggered automatically to perform the analysis. Once completed, the robot retrieves the analyzed beads from the XRF spectrometer and discards them into a bin. This seamless automation streamlines the entire process, enabling consistent, high-throughput operation with minimal operator intervention.
Automation and Usability
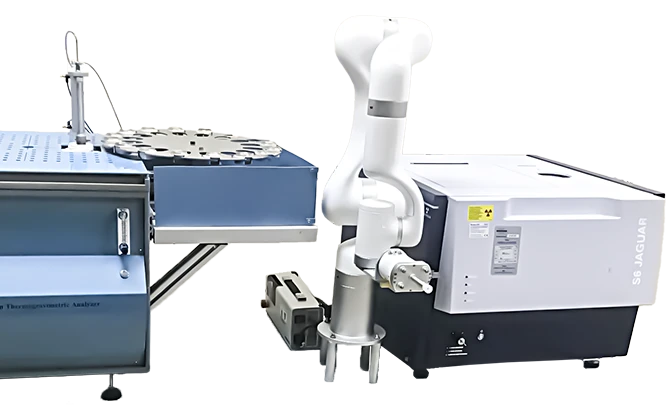
Energy Efficiency
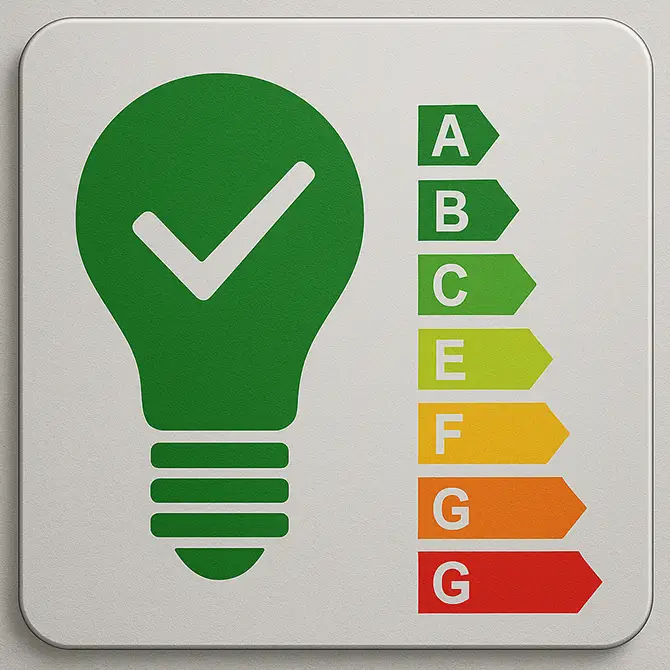
Energy Efficiency
The system requires only 2 kW of power to operate a bead fusion machine with a capacity of up to 16 crucibles, offering exceptional energy efficiency compared to competitors' machines, which typically require 5 kW of power for a 6-bead capacity. This significantly reduces energy consumption and lowers air conditioning demands, making it both cost-effective and environmentally friendly.
Energy Efficiency
The system requires only 2 kW of power to operate a bead fusion machine with a capacity of up to 16 crucibles, offering exceptional energy efficiency compared to competitors' machines, which typically require 5 kW of power for a 6-bead capacity. This significantly reduces energy consumption and lowers air conditioning demands, making it both cost-effective and environmentally friendly.
Improved Analytical Precision
Automated flux blank correction ensures consistent and accurate LOI/LOF measurements for every batch.
Improved Analytical Precision
Automated flux blank correction ensures consistent and accurate LOI/LOF measurements for every batch.
Improved Analytical Precision
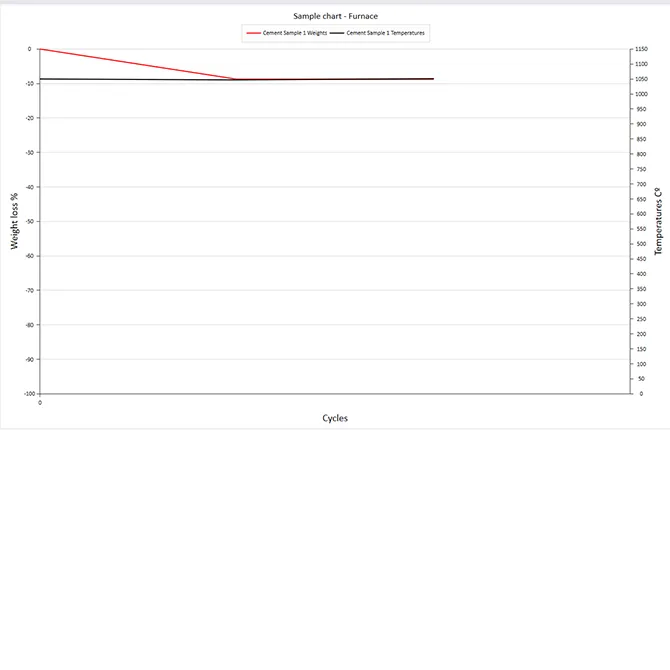
No Sample Drying Required
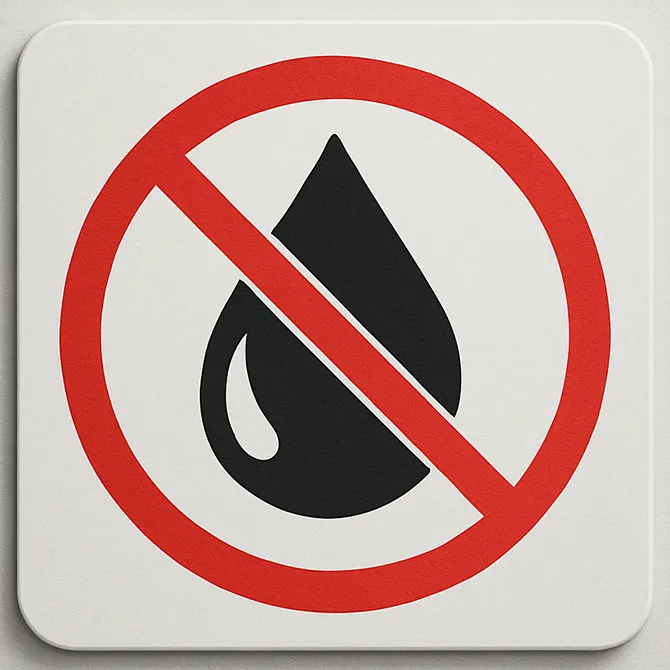
No Sample Drying Required
Samples can be fused directly without the need for pre-drying, as any moisture present evaporates during the fusion process and is accounted for as part of the Loss-On-Ignition, ensuring it does not affect the accuracy of the XRF results. This significantly reduces preparation time and enhances laboratory efficiency.
No Sample Drying Required
Samples can be fused directly without the need for pre-drying, as any moisture present evaporates during the fusion process and is accounted for as part of the Loss-On-Ignition, ensuring it does not affect the accuracy of the XRF results. This significantly reduces preparation time and enhances laboratory efficiency.
Versatility for Multiple Applications
The same instrument can also function as a thermogravimetric analyzer (TGA) with an auto-loader, without requiring the fusion process. This capability allows it to determine moisture, volatile matter, and ash content, or to operate as a dedicated LOI analyzer, providing a flexible TGA solution for various analytical needs, such as coal analysis using quartz crucibles and other applications.
Versatility for Multiple Applications
The same instrument can also function as a thermogravimetric analyzer (TGA) with an auto-loader, without requiring the fusion process. This capability allows it to determine moisture, volatile matter, and ash content, or to operate as a dedicated LOI analyzer, providing a flexible TGA solution for various analytical needs, such as coal analysis using quartz crucibles and other applications.
Versatility for Multiple Applications
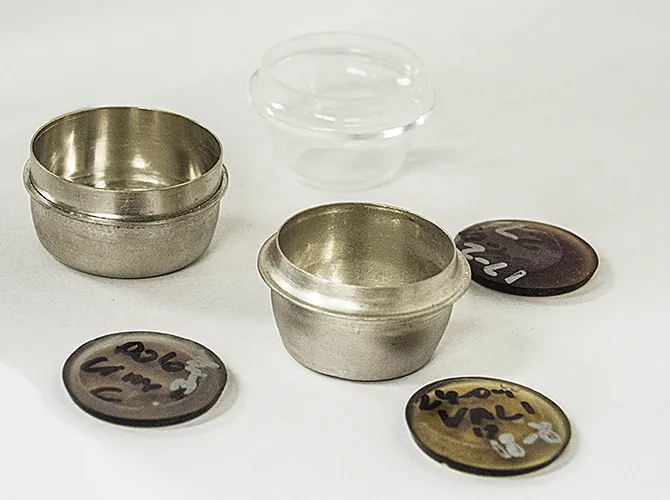
Intuitive and Customizable Windows-Based Software
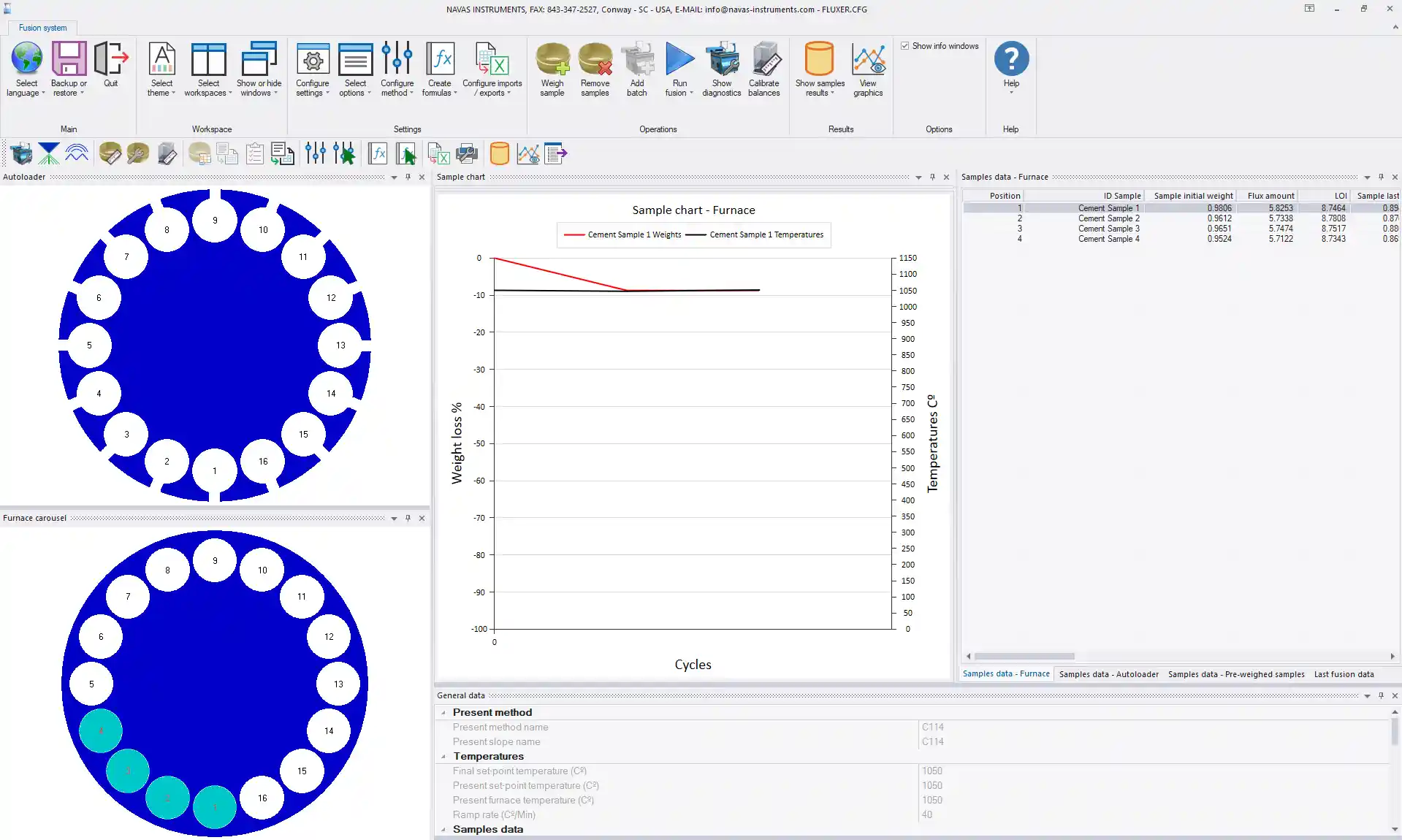
Intuitive and Customizable Windows-Based Software
The system features user-friendly Windows-based operational software designed for maximum convenience and efficiency. A ribbon bar at the top provides one-click access to the most common tasks, streamlining workflows. The interface includes panels that can be floated, docked, or tabbed, allowing users to customize their workspace layout. Additionally, the software offers configurable colors and themes, enabling users to tailor the appearance to their preferences, enhancing both usability and comfort.
The software includes a powerful database with sorting and filtering capabilities.
The software includes robust data export capabilities, allowing results to be automatically exported to text, CSV (comma-separated values), or Excel files that can be used directly or imported into LIMS (Laboratory Information Management Systems). Additionally, raw sample data can be exported in Excel format, providing comprehensive information such as times, weights, and other relevant details for all samples, ensuring seamless data management and integration.
The software features a detailed chart for each bead, providing real-time monitoring of sample weights and stability throughout the process.
Intuitive and Customizable Windows-Based Software
The system features user-friendly Windows-based operational software designed for maximum convenience and efficiency. A ribbon bar at the top provides one-click access to the most common tasks, streamlining workflows. The interface includes panels that can be floated, docked, or tabbed, allowing users to customize their workspace layout. Additionally, the software offers configurable colors and themes, enabling users to tailor the appearance to their preferences, enhancing both usability and comfort.
The software includes a powerful database with sorting and filtering capabilities.
The software includes robust data export capabilities, allowing results to be automatically exported to text, CSV (comma-separated values), or Excel files that can be used directly or imported into LIMS (Laboratory Information Management Systems). Additionally, raw sample data can be exported in Excel format, providing comprehensive information such as times, weights, and other relevant details for all samples, ensuring seamless data management and integration.
The software features a detailed chart for each bead, providing real-time monitoring of sample weights and stability throughout the process.
Important Notice
Aluminum oxide analysis results in competitors' electric furnaces are often compromised when using flux containing 0.5% lithium bromide, which significantly impacts the accuracy of aluminum oxide measurements in XRF analysis. In contrast, our instrument utilizes only a minimal amount of non-wetting agent, highly diluted in water, applied precisely at the very end of the fusion process. This innovative approach ensures exceptional accuracy in aluminum oxide analysis with our system.
Important Notice
Aluminum oxide analysis results in competitors' electric furnaces are often compromised when using flux containing 0.5% lithium bromide, which significantly impacts the accuracy of aluminum oxide measurements in XRF analysis. In contrast, our instrument utilizes only a minimal amount of non-wetting agent, highly diluted in water, applied precisely at the very end of the fusion process. This innovative approach ensures exceptional accuracy in aluminum oxide analysis with our system.
High aluminum accuracy enabled by flux that does not require releasing agent
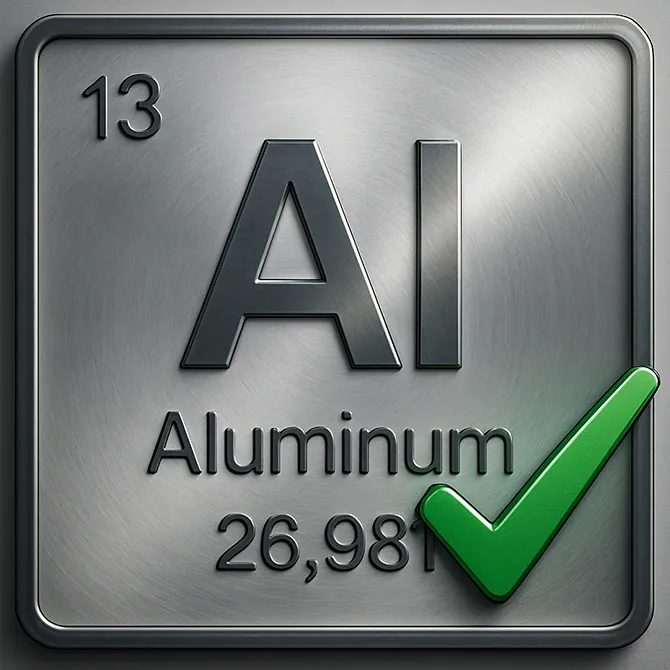
Repeatability Results of Cement Samples
Sample ID | Na2O (%) | MgO (%) | Al2O3 (%) | SiO2 (%) | P2O5 (%) | SO3 (%) | K2O (%) | CaO (%) | TiO2 (%) | Mn2O3 (%) | Fe2O3 (%) | SrO (%) | ZnO (%) | CO2 (%) | Cl (%) | Flux (g) | LOI (%) | Sample (g) | Sum (%) |
---|---|---|---|---|---|---|---|---|---|---|---|---|---|---|---|---|---|---|---|
Cement A1 | 0.06 | 2.58 | 4.38 | 18.46 | 0.14 | 2.94 | 0.56 | 58.58 | 0.25 | 0.14 | 3.14 | 0.04 | 0.04 | 8.38 | 0.02 | 6.1858 | 8.38 | 1.017 | 99.6961 |
Cement A2 | 0.09 | 2.6 | 4.34 | 18.43 | 0.13 | 2.96 | 0.57 | 58.54 | 0.25 | 0.14 | 3.15 | 0.04 | 0.03 | 8.34 | 0.01 | 5.8407 | 8.34 | 0.974 | 99.6246 |
Cement A3 | 0.07 | 2.62 | 4.44 | 18.45 | 0.13 | 2.96 | 0.56 | 58.51 | 0.26 | 0.14 | 3.16 | 0.04 | 0.03 | 8.46 | 0.01 | 5.7274 | 8.46 | 0.983 | 99.8466 |
Cement A4 | 0.06 | 2.6 | 4.33 | 18.46 | 0.14 | 2.97 | 0.56 | 58.73 | 0.25 | 0.14 | 3.14 | 0.04 | 0.04 | 8.43 | 0.01 | 6.3705 | 8.43 | 1.059 | 99.9068 |
Cement A5 | 0.09 | 2.56 | 4.33 | 18.34 | 0.14 | 2.94 | 0.56 | 58.45 | 0.25 | 0.14 | 3.14 | 0.04 | 0.03 | 8.35 | 0.01 | 5.7313 | 8.35 | 0.971 | 99.3861 |
Technical Specifications of FTA-2000 Multi-Sample XRF Fusion System
Designed for Precision, Flexibility, and Productivity
Specification | Details |
---|---|
Number of Beads | Configurations available for 4, 6, 8, 10, 12, 14, or 16 beads; easily expandable |
Software Features |
Unlimited fusion programs Open database connectivity Customizable reports Data export to TXT, CSV, and XLS formats for LIMS or Microsoft Excel integration |
LOI/LOF Range | Weight loss/gain range: 0–100% |
Balance Sensitivity | 0.1 mg |
LOI/LOF Precision | Determined by balance resolution |
Temperature Range | 200–1150 °C with ±1 °C accuracy |
Instrument Control | Operable via desktop or laptop PC with USB interface |
Dimensions |
Width: 21.81 inches (55.4 cm) Length: 23.62 inches (60 cm) Height: 22.44 inches (57 cm) Auto-loader height: 13 inches (33 cm) |
Weight | 133 lb (60 kg) |
Power Requirements | 220V AC, 2 kW |